GPRS Project Manager David Castro led a comprehensive infrastructure visualization effort that combined Video Pipe Inspection (VPI) and 3D laser scanning to deliver a complete understanding of the site conditions before any construction began.
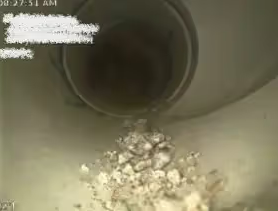
GPRS Gives Critical Sewer & Structural Infrastructure Insights to a California Warehouse
GPRS Uncovers Critical Sewer and Structural Insights for California Distribution Warehouse Renovation
When a seasoned property investment client acquired a 100,000-square-foot distribution warehouse in Northern California, they once again turned to GPRS to uncover hidden infrastructure issues and provide precise as-built documentation for renovation planning. GPRS Project Manager David Castro led a comprehensive infrastructure visualization effort that combined Video Pipe Inspection (VPI) and 3D laser scanning to deliver a complete understanding of the site conditions before any construction began.
The client, a repeat GPRS customer, frequently purchases, remodels, and repurposes commercial and industrial properties. Their goal is consistent: avoid unexpected costs, maintain construction timelines, and ensure safety throughout the renovation process. According to Castro, GPRS services allow these clients to “know what they’re walking into, so they don’t walk into any unexpected expenses or problems.”
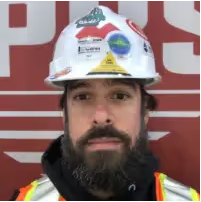
Sewer System Condition Assessment with Video Pipe Inspection
The first step in GPRS’ evaluation of the warehouse involved a detailed inspection of the interior sewer system using its video pipe inspection service. This process enables GPRS to both assess the physical condition of underground piping and precisely map its layout, a critical requirement for any remodel involving plumbing system modifications or expansions.
During a VPI, NASSCO-certified Project Managers deploy remote-controlled robotic crawlers and push-fed camera systems, equipped with high-resolution CCTV and sondes. These sondes emit electromagnetic signals that can be detected from the surface, allowing the project team to track the position of the camera underground with EM locators in real time.
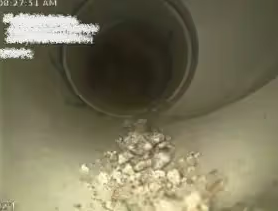
GPRS’ Castro used CCTV cameras as part of his sewer inspection. He mapped the sewer lines for a 100,000 s.f. warehouse facility so the facility manager could plan upgrades and repairs.
This dual inspection and mapping approach results in a detailed, NASSCO-compliant WinCan report. Each defect is cataloged with location data, severity rankings, and supporting video or photo documentation. Facilities managers benefit from this actionable intelligence, enabling them to address critical issues such as root intrusion, clogs, cross bores, or inflow and infiltration, with confidence in both the diagnosis and repair planning.
In the case of this California facility, Castro reported that the sewer system was in relatively good condition. However, he did find that several cleanouts contained debris that appeared to have been intentionally introduced. Despite this minor anomaly, the system as a whole was serviceable and structurally sound.
“For the most part, the sewer system was actually fairly new, and it looked to be in good condition,” Castro said. “But that’s not always the case. Most of the time, clients share stories like, ‘We bought a property across town, and within a month, we had serious sewer backup issues.’ This inspection is about giving them clarity—whether they need to replace anything or if they’re in the clear.”
3D Laser Scanning and As-Built Modeling with Matterport Pro 3
Following the VPI, GPRS performed a complete 3D laser scan of the warehouse using a Matterport Pro 3 scanner. This system captures high-resolution, full-color digital twins of built environments with 20mm accuracy at up to 10 meters range.
With this data, GPRS’ in-house Mapping & Modeling Team produced point clouds, CAD drawings, a 3D BIM model, and a virtual WalkThru 3D tour of the entire building. These deliverables provide facilities teams and design consultants with the spatial intelligence needed to support accurate and efficient renovations.

GPRS’ 3D laser scans allowed our Mapping & Modeling Team to create a detailed 3D model, 2D CAD drawings and a WalkThru 3D virtual tour of the facility so they could plan, design, and collaborate more effectively.
The Matterport-based visualization enabled the client to evaluate existing building layouts, plan new restroom installations, and assess the impact of potential floor plan changes. It also served as a valuable resource for coordination between architects, engineers, and contractors during the early stages of project planning.
Castro noted the importance of this digital documentation in supporting design decisions, especially related to plumbing.
“Obviously with that project, they kind of need to know where the existing mainline is running through the building and then the depth,” he said. “So that way, they know what elevations they need to hit and all of that. Without us being there, they would have no idea where the sewer system is, or where to tie in. Their engineers would have no idea how to draw that plan up to get it to spec.”
Integrated Infrastructure Visualization for Confident Planning
GPRS’ combined VPI and laser scanning services provided the client with a fully integrated infrastructure visualization solution. This approach mitigates renovation risks by delivering detailed data on existing conditions—above and below ground.
By visualizing invisible infrastructure, GPRS enables facilities managers, general contractors, and engineers to make informed decisions, reduce change orders, and avoid costly surprises. The company’s full suite of services, including utility locating, concrete scanning, leak detection, and advanced 3D modeling, is designed to support projects from initial due diligence through final construction.
From sewer lines to skyscrapers, GPRS continues to fulfill its mission: Intelligently Visualize The Built World®.
What can we help you visualize?